網站首頁
Website Home
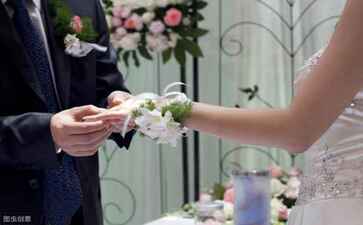
浙江榮通防爆電器設備有限公司位于余江縣,浙江榮通防爆電器設備有限公司www.gbqdiw.com.cn經營范圍含:冰箱清洗、手機通訊、防水、衛生設施建設、電子電工產品制造設備、堅果、扎染、食品、罐頭食品、冷光源(依法須經批準的項目,經相關部門批準后方可開展經營活動)。。
浙江榮通防爆電器設備有限公司遵照黨中央、國務院關于國有企業深化改革的戰略部署,我們將緊密圍繞國資委提出的做大、做強企業的核心要求,堅定不移地推動企業改革進程。我們將進一步優化產業結構,合理配置資源,以提升企業的核心競爭力為關鍵,全面提升企業的整體素質和經營能力。同時,我們將積極面向國際、國內兩個市場,努力開拓新的發展空間,向著更加遠大、宏偉的目標不斷奮斗,為實現企業的可持續發展和國家的繁榮富強貢獻力量。
浙江榮通防爆電器設備有限公司在發展中注重與業界人士合作交流,強強聯手,共同發展壯大。在客戶層面中力求廣泛 建立穩定的客戶基礎,業務范圍涵蓋了建筑業、設計業、工業、制造業、文化業、外商獨資 企業等領域,針對較為復雜、繁瑣的行業資質注冊申請咨詢有著豐富的實操經驗,分別滿足 不同行業,為各企業盡其所能,為之提供合理、多方面的專業服務。
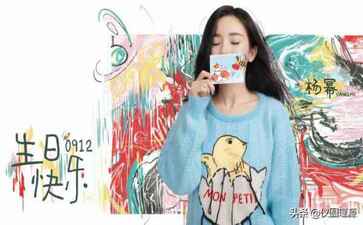
浙江榮通防爆電器設備有限公司秉承“質量為本,服務社會”的原則,立足于高新技術,科學管理,擁有現代化的生產、檢測及試驗設備,已建立起完善的產品結構體系,產品品種,結構體系完善,性能質量穩定。
浙江榮通防爆電器設備有限公司是一家具有完整生態鏈的企業,它為客戶提供綜合的、專業現代化裝修解決方案。為消費者提供較優質的產品、較貼切的服務、較具競爭力的營銷模式。
核心價值:尊重、誠信、推崇、感恩、合作
經營理念:客戶、誠信、專業、團隊、成功
服務理念:真誠、專業、精準、周全、可靠
企業愿景:成為較受信任的創新性企業服務開放平臺
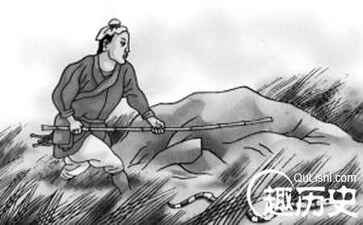